Description
Diameters:Â Stocked in the pre-hardened condition (30-34 HRC) can be heat treated to 50-53 HRC
Plates:Â Stocked in the annealed condition. Can be heat treated to 50-53 HRC.
Applications include:
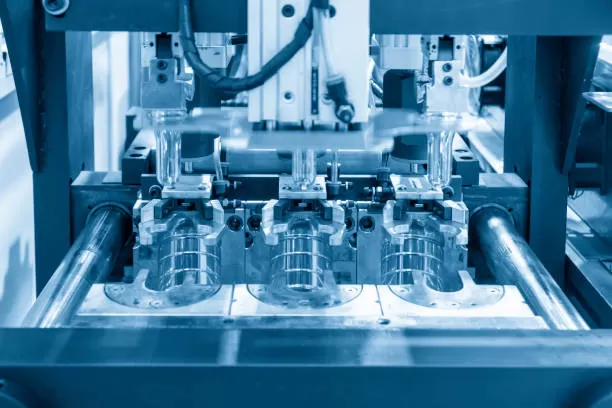
Ultra mirror finish plastic molds
Lens
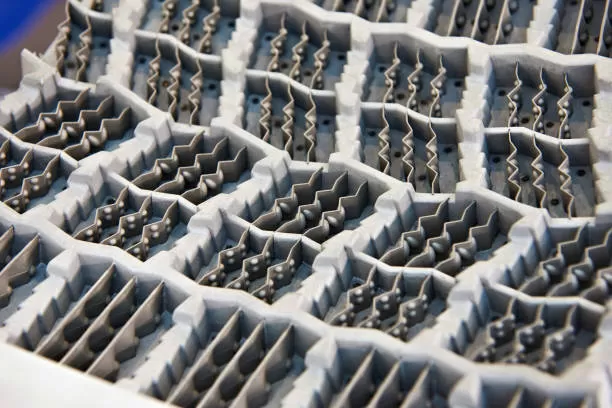
Ultra-hard, Corrosion-resistance plastic molds
Medical Instruments, Cosmetic container, Food container
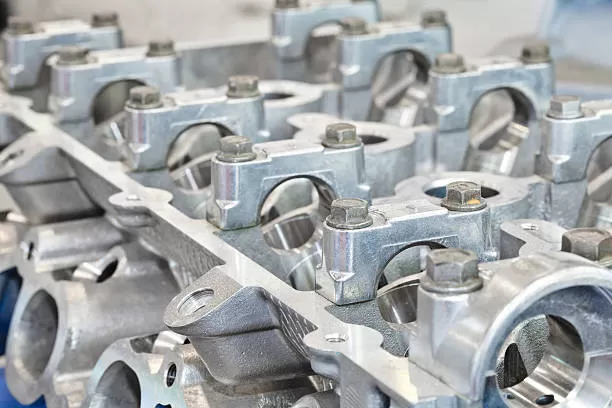
Resin PMMA, PC, PP, PS, PVC, PE, PF,
Flame resisting compound added resin
Unique Characteristics
- Excellent corrosion resistance
- High hardness: maximum 53 HRC is obtained
- Superb mirror-finish surface
- Minimal distortion, less than 0.03% after heat treatment
- Excellent internal matrix by ESR
- Uniform texture surface by photo etching and electrical discharge machining
Product Brochure
Chemical Composition
Mechanical Properties
Mechanical Properties
Thermal Expansion Coefficient
Thermal Conductivity
Longitudinal Elastic Modulus
Density
Specific Heaty
Physical Properties
Mirror Grade Finish
Heat Treatment
Hardened-Tempered Hardness Maximum hardness of 53HRC is obtained.  QuenchingÂ
 Tempering Double tempering is recommended for both low and high temperature tempering.Â
 Notes:
- For higher corrosion resistance, tempering should be carried out at temperatures of 400°C or lower.
- To prevent cracking in EDM, tempering is recommended at 490 to 510°C
- When aging dimensional stability is deemed important, carry out low-temperature tempering at 200 to 400°C or sub-zero processing.
Dimensional Change Dimensional change is the smallest by tempering about 300°C Â
Welding Guidelines
Build-up Welding Procedures
Mechanical Properties
Thermal Expansion Coefficient
Thermal Conductivity
Longitudinal Elastic Modulus
Density
Specific Heaty
Mirror Grade Finish
Heat Treatment
Hardened-Tempered Hardness Maximum hardness of 53HRC is obtained.  QuenchingÂ
 Tempering Double tempering is recommended for both low and high temperature tempering.Â
 Notes:
- For higher corrosion resistance, tempering should be carried out at temperatures of 400°C or lower.
- To prevent cracking in EDM, tempering is recommended at 490 to 510°C
- When aging dimensional stability is deemed important, carry out low-temperature tempering at 200 to 400°C or sub-zero processing.
Dimensional Change Dimensional change is the smallest by tempering about 300°C Â
Build-up Welding Procedures