Description
DH2F is a modified H-13, prehardened 37-41 HRC.
Applications include:
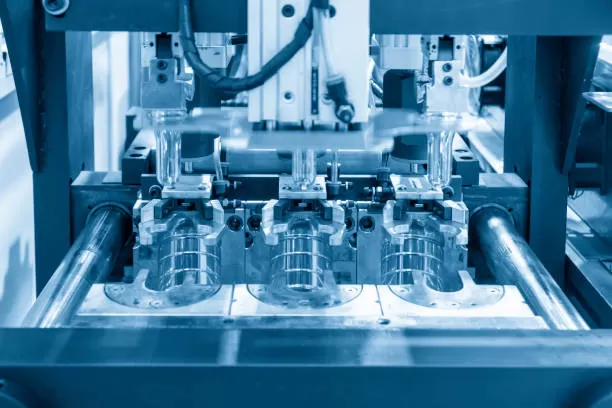
Plastic Molds
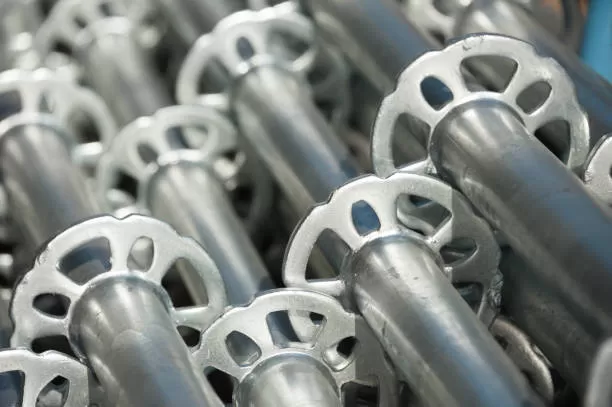
Zinc Diecasting Dies
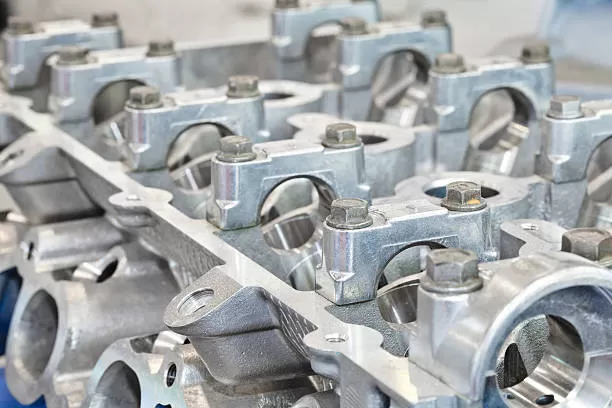
Short Run Aluminum Diecasting Dies
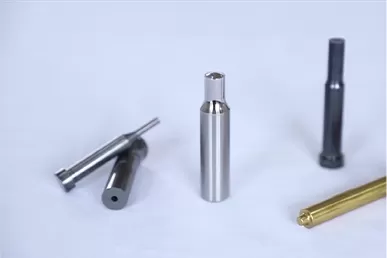
Plunger Tips & Sprue Bushings
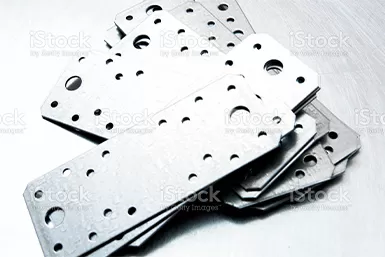
Die Plate Strippers
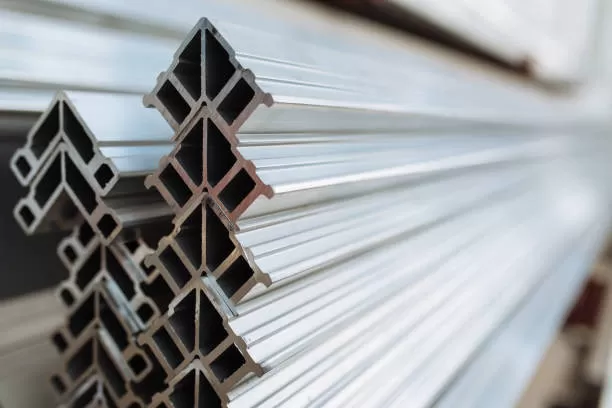
Dies for Aluminum Extrusions
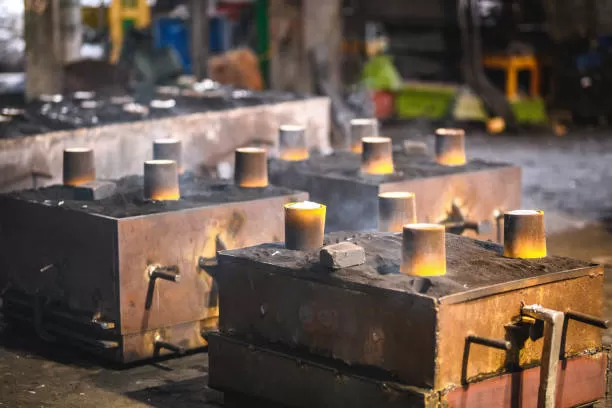
Patterns & Core Boxes
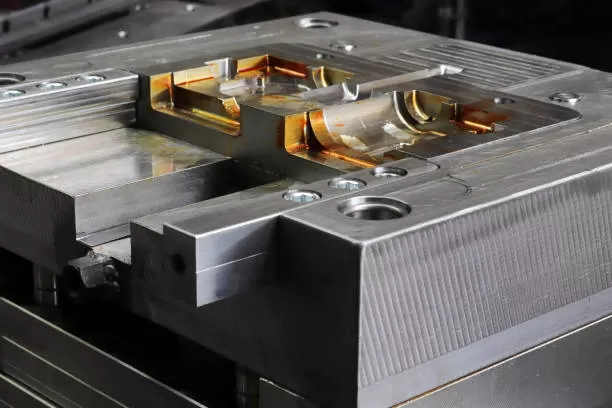
Others
Unique Characteristics
- 38-42 HRc hardness.
- Through hardened for exceptional dimensional stability.
- Cuts mold making costs by reducing man hours required for machining.
- Classified as a “free-machining” steel.
- Ideal for complex, precision molds and parts susceptible to distortion and/or deformation without needing additional heat-treating.
- Ideal for Ion-nitriding.
Product Brochure
BENEFITS
the data below.
Machining:
DH2F has a machine rating of 65 out of 100, with 100 being the best rating for pre-hardened mold steels.
(For comparison, P20 at 30 HRc has a machine rating of 50.)
DH2F’s superior machinability means extended tool life.
A positive rake cutter with a concave face and chip breaking edge works best.
Example Tool Life of Face Milling Cutter
Example of Tool Life of HSS Drill Bit
Cutting Parameters
Tool Material | Tool Shape | Cutting Fluid | Feed | Cut | Cutting Speed | Test Piece Size | Hardness | Tool LIfe End Point | |
Face Milling Cutter | M20 | NP-100R | None | 0.003″ | 0.059″ | 66-165 | 80″x50″x200″ | 40 | V MAX=0.012″ |
Drill Bit | SKHS1 | 0.394” dia. tapered-shank drill a=118 | None | 0.004″ | 1.181″ deep hole | 20-40 | 80″x50″x200″ | 40 | Tool Erosion |
Chip Shape
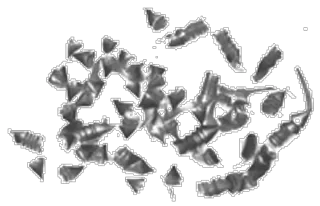
D2HF (Modified H-13, pre-hardened)
H-13
Cutting Parameters
Tool | SKH51 0.394” dia., tapered-shank drill a=118° |
Feed | 0.0039″/rev |
Hole Depth | 1.181″ |
Cutting Speed | 25m/min |
Test PIece Hardness | 40 HRc |
Test Piece Size | 3.937″ x 7.874″ x 11.811″ |
Surface Testing
Surface treating gives DH2F enhanced abrasion and corrosion resistance.
Abrasion Speed (ft/s) | Abrasion loss (mm²kgfx10-7) | |
DH2F | H13 | |
0.656 | 3.76 | 3.50 |
1.6728 | 5.24 | 3.56 |
3.0832 | 3.50 | 5.24 |
5.34663 | 3.03 | 5.56 |
6.4616 | 4.04 | 5.24 |
7.8064 | 4.61 | 5.24 |
Test Machine | Ohgoshi method abrasion test apparatus |
Abrasion Load | 656ft |
Final Load | 1.4982lbs |
Mating Material (disk) | D2.HRc57 |
Abrasion Speed | 0.656 to 7.872 ft./sec. |
Test Piece Hardness | HRc 42 |
Erosion Resisitance
Weight Before Test (gr) |
Weight After | Erosion Loss | ||
Test (gr) | (gr) | (%) | ||
D2HF | 27.33 | 23.18 | 4.15 | 15.2 |
H13 | 27.12 | 23.39 | 3.73 | 13.9 |
Erosion testing: An annealed .591″ dia. x .787″ sample is weighed before and
after soaking in an aluminum bath at 1,292°F for 30 hours.
Polishing:
DH2F is a resulfurised steel and sulfur can affect polishing. We recommend contacting International Mold Steel if you are considering SPI #2 or better polish.
Welding:
The same filler material that is used for typical H13 is recommended for DH2F.
- Pre-heat temperature: 575-650°F
- Post-heat temperature: 750-1000°F
MECHANICAL PROPERTIES
Test piece size: | |
Tension test: | .315″ dia. X 3.543″ |
Charpy impact test: | JIS NO. 3 test piece (R1, .079″ hole depth) obtained from the material in the rolling direction. |
PHYSICAL PROPERTIES
68~212°F | 68~392°F | 68~572°F | 68~752°F | 68~932°F | 68~1,112°F | 68~1,292°F | |
DH2F | 4.94 | 6.00 | 6.61 | 7.00 | 7.28 | 7.61 | 7.72 |
H13 | 4.78 | 5.61 | 6.33 | 6.78 | 7.11 | 7.39 | 7.56 |
Microstructure
Hardening: 1886°F, air-cooling
Tempering: 1166°F x 1 hr.
Hardness: 40 HRc
Tempering / Hardness Curve
The material, as delivered, does not require heat-treating. This data is presented merely for reference.
CHEMICAL COMPOSITION
Chemical Composition (%) of D2HF
Corresponding JIS Spec | C | Si | Mn | Cr | Mo | V | Free Machining Elements |
– | 0.32 – 0.42 | 0.5 | 0.5 | 4.50 – 5.50 | 1.00 – 1.50 | 0.40 – 1.20 | Added |
the data below.
Machining:
DH2F has a machine rating of 65 out of 100, with 100 being the best rating for pre-hardened mold steels.
(For comparison, P20 at 30 HRc has a machine rating of 50.)
DH2F’s superior machinability means extended tool life.
A positive rake cutter with a concave face and chip breaking edge works best.
Example Tool Life of Face Milling Cutter
Example of Tool Life of HSS Drill Bit
Cutting Parameters
Tool Material | Tool Shape | Cutting Fluid | Feed | Cut | Cutting Speed | Test Piece Size | Hardness | Tool LIfe End Point | |
Face Milling Cutter | M20 | NP-100R | None | 0.003″ | 0.059″ | 66-165 | 80″x50″x200″ | 40 | V MAX=0.012″ |
Drill Bit | SKHS1 | 0.394” dia. tapered-shank drill a=118 | None | 0.004″ | 1.181″ deep hole | 20-40 | 80″x50″x200″ | 40 | Tool Erosion |
Chip Shape
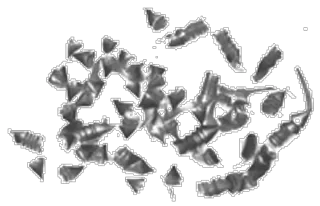
D2HF (Modified H-13, pre-hardened)
H-13
Cutting Parameters
Tool | SKH51 0.394” dia., tapered-shank drill a=118° |
Feed | 0.0039″/rev |
Hole Depth | 1.181″ |
Cutting Speed | 25m/min |
Test PIece Hardness | 40 HRc |
Test Piece Size | 3.937″ x 7.874″ x 11.811″ |
Surface Testing
Surface treating gives DH2F enhanced abrasion and corrosion resistance.
Abrasion Speed (ft/s) | Abrasion loss (mm²kgfx10-7) | |
DH2F | H13 | |
0.656 | 3.76 | 3.50 |
1.6728 | 5.24 | 3.56 |
3.0832 | 3.50 | 5.24 |
5.34663 | 3.03 | 5.56 |
6.4616 | 4.04 | 5.24 |
7.8064 | 4.61 | 5.24 |
Test Machine | Ohgoshi method abrasion test apparatus |
Abrasion Load | 656ft |
Final Load | 1.4982lbs |
Mating Material (disk) | D2.HRc57 |
Abrasion Speed | 0.656 to 7.872 ft./sec. |
Test Piece Hardness | HRc 42 |
Erosion Resisitance
Weight Before Test (gr) |
Weight After | Erosion Loss | ||
Test (gr) | (gr) | (%) | ||
D2HF | 27.33 | 23.18 | 4.15 | 15.2 |
H13 | 27.12 | 23.39 | 3.73 | 13.9 |
Erosion testing: An annealed .591″ dia. x .787″ sample is weighed before and
after soaking in an aluminum bath at 1,292°F for 30 hours.
Polishing:
DH2F is a resulfurised steel and sulfur can affect polishing. We recommend contacting International Mold Steel if you are considering SPI #2 or better polish.
Welding:
The same filler material that is used for typical H13 is recommended for DH2F.
- Pre-heat temperature: 575-650°F
- Post-heat temperature: 750-1000°F
Test piece size: | |
Tension test: | .315″ dia. X 3.543″ |
Charpy impact test: | JIS NO. 3 test piece (R1, .079″ hole depth) obtained from the material in the rolling direction. |
68~212°F | 68~392°F | 68~572°F | 68~752°F | 68~932°F | 68~1,112°F | 68~1,292°F | |
DH2F | 4.94 | 6.00 | 6.61 | 7.00 | 7.28 | 7.61 | 7.72 |
H13 | 4.78 | 5.61 | 6.33 | 6.78 | 7.11 | 7.39 | 7.56 |
Microstructure
Hardening: 1886°F, air-cooling
Tempering: 1166°F x 1 hr.
Hardness: 40 HRc
Tempering / Hardness Curve
The material, as delivered, does not require heat-treating. This data is presented merely for reference.
Chemical Composition (%) of D2HF
Corresponding JIS Spec | C | Si | Mn | Cr | Mo | V | Free Machining Elements |
– | 0.32 – 0.42 | 0.5 | 0.5 | 4.50 – 5.50 | 1.00 – 1.50 | 0.40 – 1.20 | Added |